One Stop Service for Artificial Twigs Project
Service: CNC, Die casting, Surface finish ( Powder coating matching the effect of bark) ,Assembly, Testing, Packing and Delivery
Material: Al6061, A380
Quantity: 1 set prototype, 3000 sets die casting parts
Lead time: CNC prototyping: 13 working days
Tooling manufacture: 30 working days
Die casting for 3000 sets: 15 working days
Powder coating: 7 working days
Assembly and packing: 15 working days
About the project
The twigs need to be installed the LEDs and wires inside, they will be assembled into a big artificial tree which will be situated at outside door throughout the year at squares of Norway, Florida and Las Vegas respectively. So the concept of the design must be well fit and waterproof, and the powder coating must be corrosion resistance.
The client requests to make 1 set prototype by CNC to check the design before starting the tooling. The prototype was manufactured by HAAS 4SS machine.
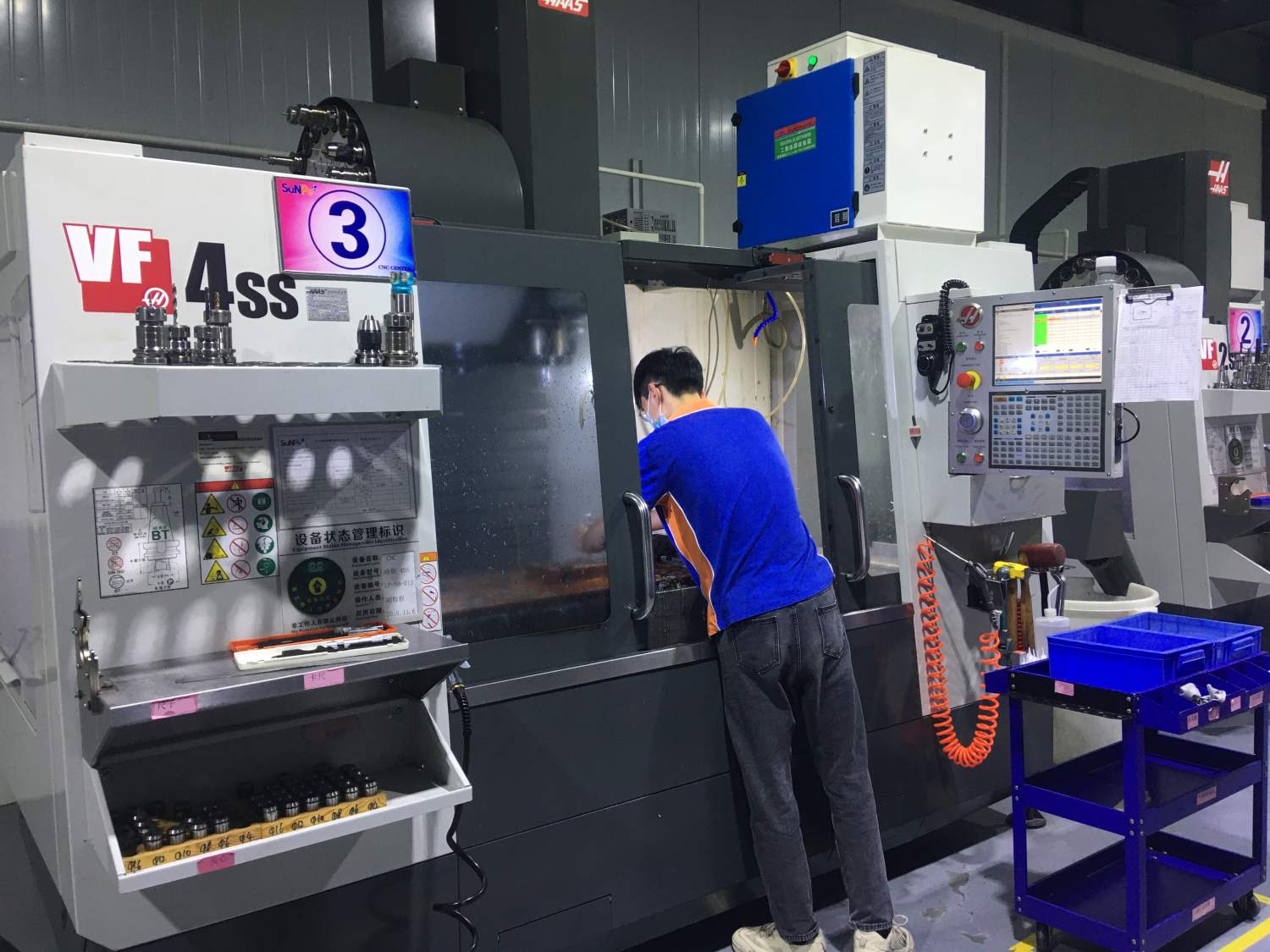
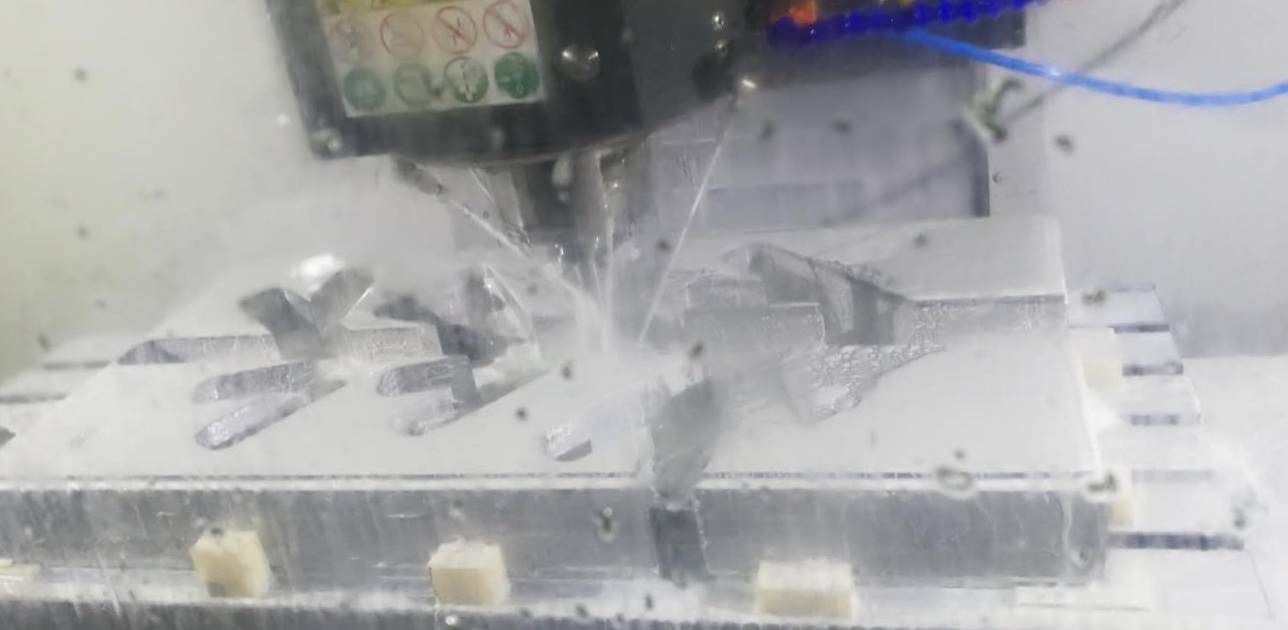
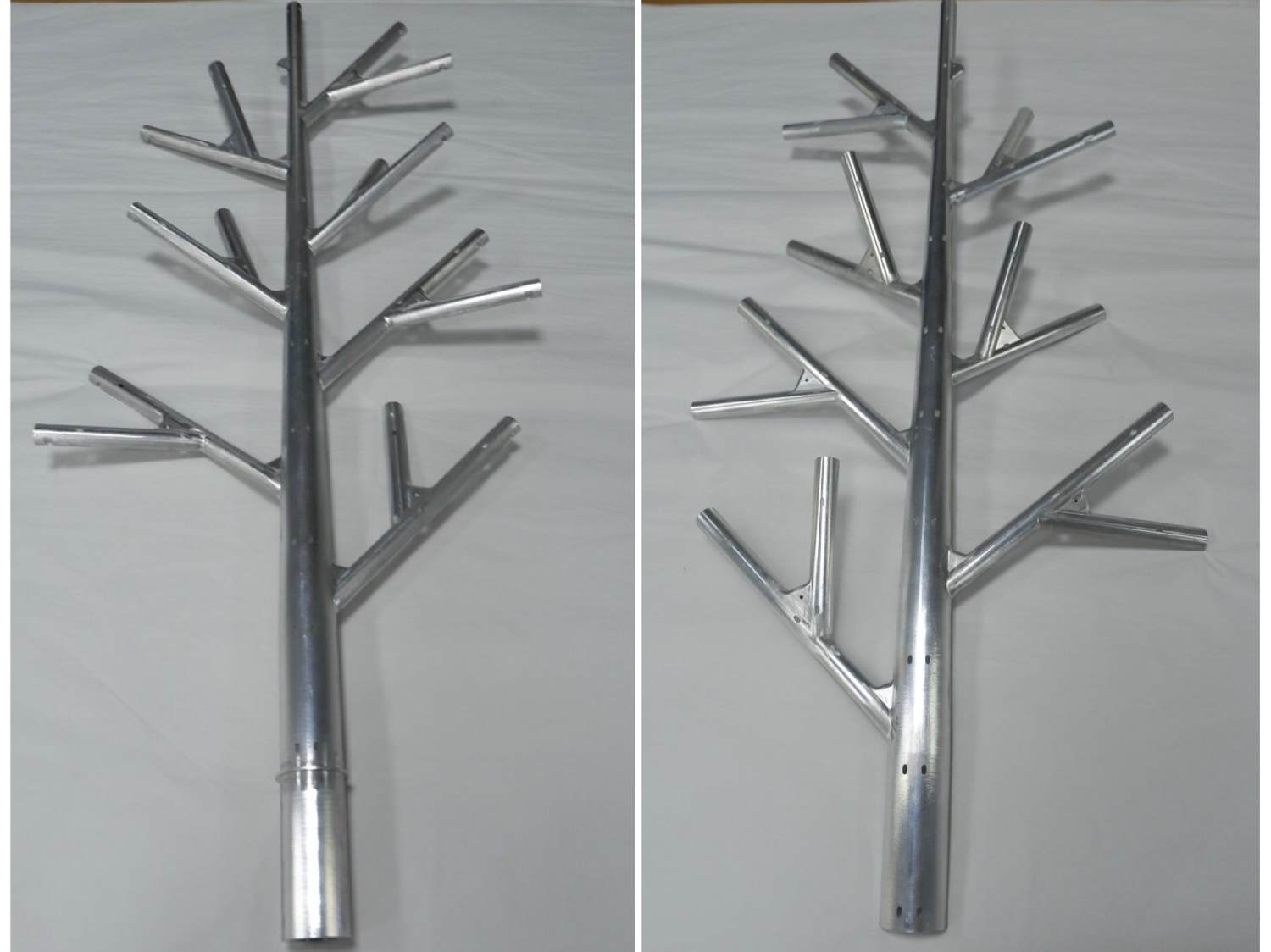
Before the volume production, we discuss and give some suggestions to our client to ensure the assembly of the parts well.
How do the production steps work?
>Step 1: Tooling making and die casting
The die casting mold is made from H13 tool steel using CNC machining and wire EDM. Several tests casting are done to confirm the accuracy of the build and adjustments are made to the tool accordingly. We send the samples make from A380 aluminum alloy to our client for confirmation first before production.
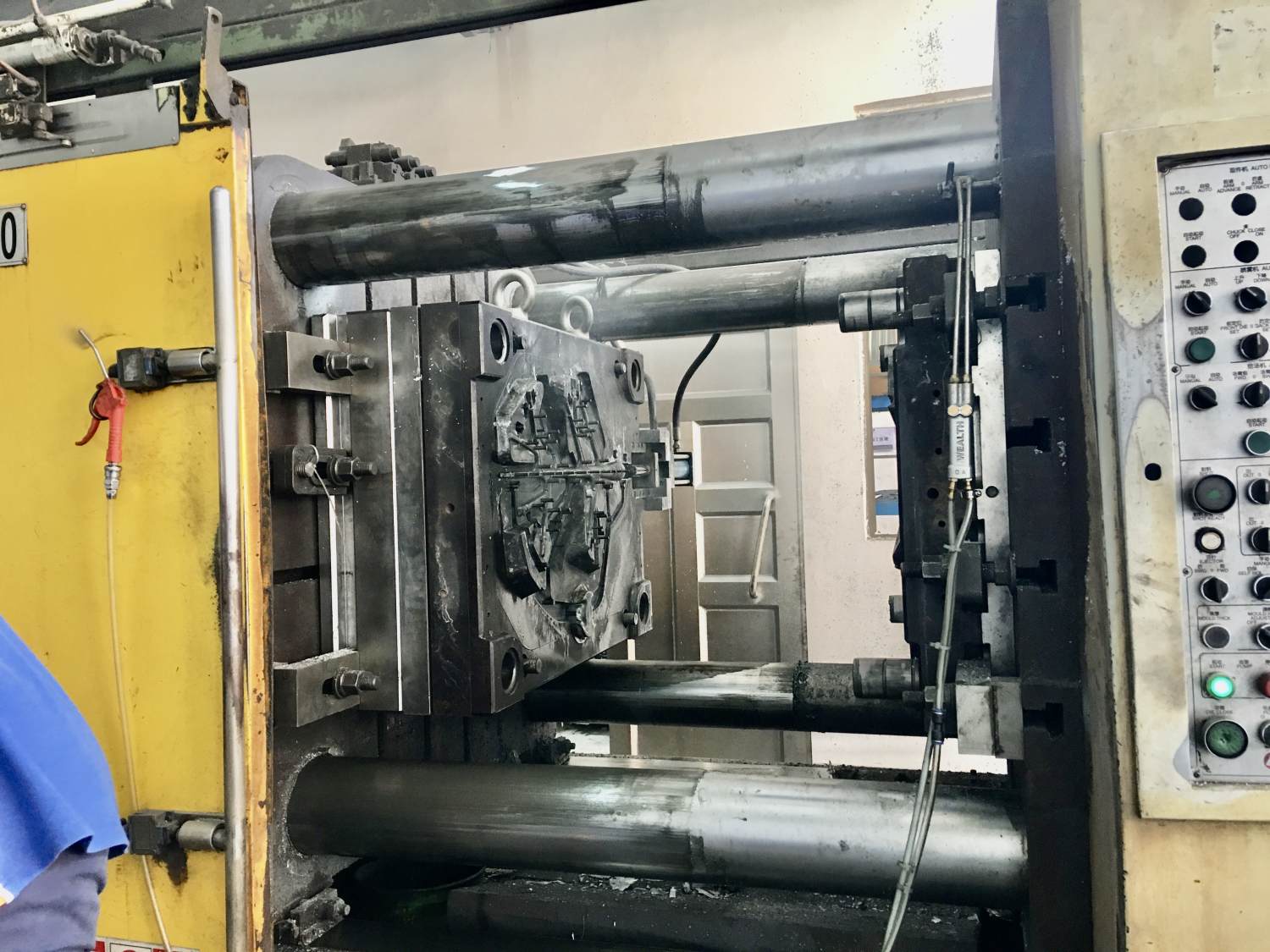
>Step 2: Surface treatment
1)Removing the flash and gate on the die casting parts.
2) Powder coating:
Screwing the top and bottom aluminum parts together before the powder coating, which can save the cost and time of the powder coating , also can keep the inside surface of the parts without coating.
Using a special cleaning tank to clean the aluminum powder and oil marks on the product surface.
Powder coating color and texture of the product should be matched the bark sample provided by our client, we make it in Antique texture which similar to the bark texture and do the color match.
>Step 3: Assembly
1) Assembling the wires and leaves provided by our client
We lay the wires flat on the workbench, and arrange the connectors in order from 1 to 15 firstly, then connect the leaf connector with the wire connector in the direction of the connector and power-on test refer to the power-on test operation guide.
After the testing pass, we use a hot air blower to heat the middle of the heat shrinkable tube until the entire heat shrinkable tube shrinks and wraps the terminal, this step can protect the wires and lights from the water.
2) Assembling the aluminum parts.
3)Doing the power-on test refer to the power-on test operation guide again to ensure all the lights are working well after the assembly.
>Step 4: Packing and Delivery
We custom-made the paper tray to package the products, which can protect well the parts to avoid any defects during the transportation.
Artificial trees showing at the squares