SuNPe has own sheet matal factory which can support projects from simple bent sheet metal prototypes to complex mechanical assemblies.
The materials commonly used in sheet metal processing are cold rolled plate (SPCC), hot rolled plate (SHCC), galvanized plate (SECC、SGCC), copper (CU) brass, aluminum plate like AL5052, stainless steel (mirror/polished, brushing surface, frosted surface).

(Sheet Metal material,steel sheet,aluminum sheet)
According to the difference of sheet metal structure, the process flow can be different steps as below:
1.Laser cutting is to use laser cutting method to cut out the structural shape of the plate on a large plate. Like CNC cutting material, laser program should be written. It can be used for various complex shape flat parts with low cost and precision of 0.1mm

(Laser cut machine)
2.Flanging: also known as pumping hole, flanging hole, is to make a slightly larger hole on a smaller base hole, re-tapping, mainly using thin plate, increase its strength and number of threads, avoid sliding teeth, its hole around normal shallow flanging, the thickness is basically unchanged.
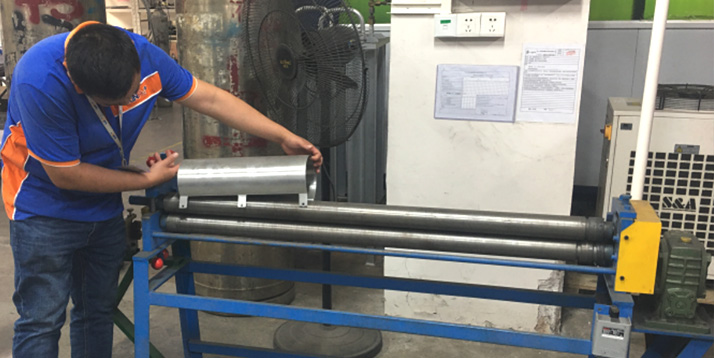
(Flanging, pumping)
3.Punching:the general punching machine has punching, cutting angle, blanking, punching bump (bump), punching tear, pumping hole, forming etc processing methods, it needs to have the corresponding die to complete the operation, the operation mainly pay attention to the position, direction.

(Punching)
4.Pressure riveting: there are mainly pressure riveting nuts, screws, bolt and so on, it is through the hydraulic pressure riveting machine or punching machine to do.

(riveting, punching)
5.Bending: bending is to fold 2D of flat parts into 3D of parts. We usually make bending die to complete it.
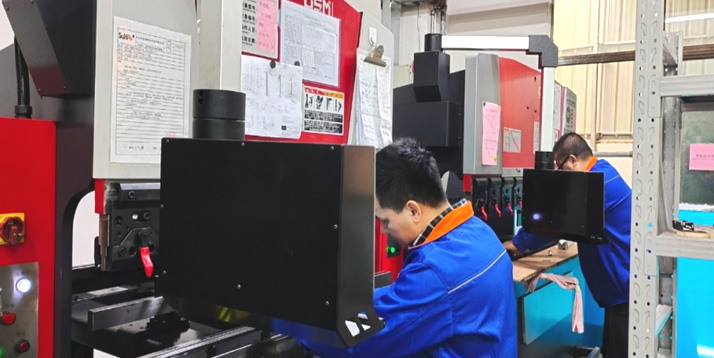
(Bending)
6.Welding: argon arc welding is common used in welding process, weld two or more parts together to achieve the purpose of assembly finished products, or the edge seam of a single part needs to be welded to make the bending edge precise to increase the folding strength.
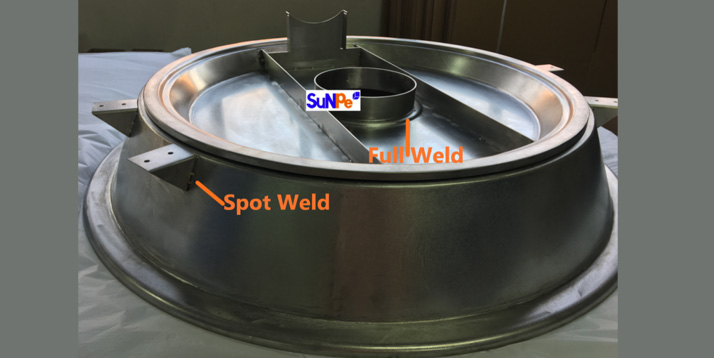
(Welding,spot weld,full weld)
7.Assembly:we also have assembly workshop to support from prototyping to low volume production. Assemble the whole product to help our customer make their design to be real.

(Assembly workshop)
If you'd like to know more about Sheet metal and our other services,please feel free to contact us.
The materials commonly used in sheet metal processing are cold rolled plate (SPCC), hot rolled plate (SHCC), galvanized plate (SECC、SGCC), copper (CU) brass, aluminum plate like AL5052, stainless steel (mirror/polished, brushing surface, frosted surface).

(Sheet Metal material,steel sheet,aluminum sheet)
According to the difference of sheet metal structure, the process flow can be different steps as below:
1.Laser cutting is to use laser cutting method to cut out the structural shape of the plate on a large plate. Like CNC cutting material, laser program should be written. It can be used for various complex shape flat parts with low cost and precision of 0.1mm

(Laser cut machine)
2.Flanging: also known as pumping hole, flanging hole, is to make a slightly larger hole on a smaller base hole, re-tapping, mainly using thin plate, increase its strength and number of threads, avoid sliding teeth, its hole around normal shallow flanging, the thickness is basically unchanged.
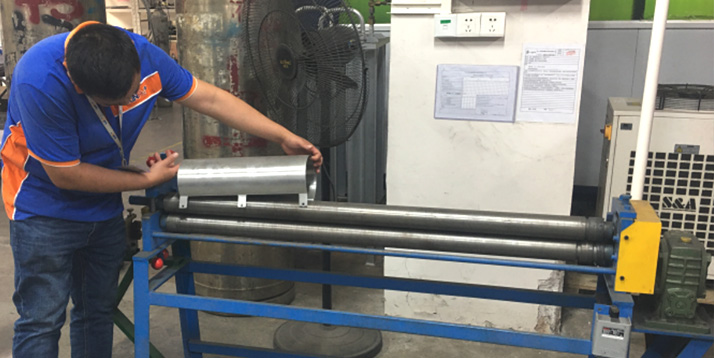
(Flanging, pumping)
3.Punching:the general punching machine has punching, cutting angle, blanking, punching bump (bump), punching tear, pumping hole, forming etc processing methods, it needs to have the corresponding die to complete the operation, the operation mainly pay attention to the position, direction.

(Punching)
4.Pressure riveting: there are mainly pressure riveting nuts, screws, bolt and so on, it is through the hydraulic pressure riveting machine or punching machine to do.

(riveting, punching)
5.Bending: bending is to fold 2D of flat parts into 3D of parts. We usually make bending die to complete it.
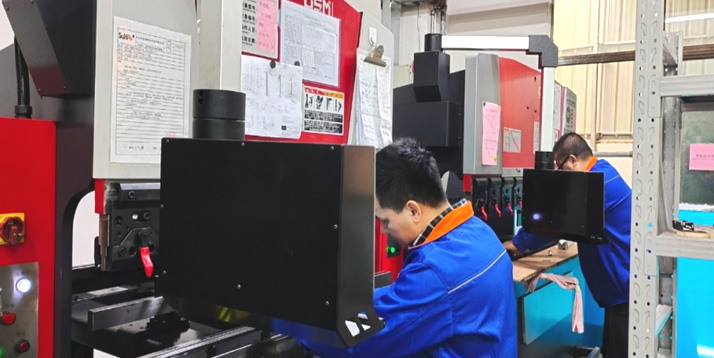
(Bending)
6.Welding: argon arc welding is common used in welding process, weld two or more parts together to achieve the purpose of assembly finished products, or the edge seam of a single part needs to be welded to make the bending edge precise to increase the folding strength.
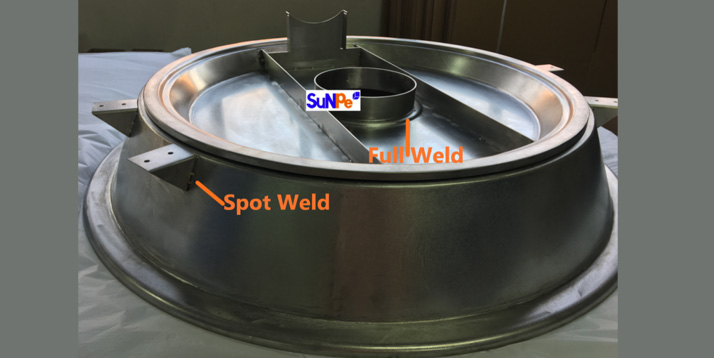
(Welding,spot weld,full weld)
7.Assembly:we also have assembly workshop to support from prototyping to low volume production. Assemble the whole product to help our customer make their design to be real.

(Assembly workshop)
If you'd like to know more about Sheet metal and our other services,please feel free to contact us.
Other news
- 1SuNPe Had a Successful Exhibition on Formnext 2018
- 2How does SuNPe help with post-machining?
- 35 Types of Metal materials for Prototyping and Production
- 4Fire Drill at new factory of SuNPe, The escort of your projects!
- 5Better Services, Better Performance, Better Life ——2019 Annual Meeting of Sales Team
- 6How Does Sheet Metal Fabrication Help In Real Life ?
- 7Quality is everything at SuNPe--new inspection equipment in 2020
- 8SuNPe Holds Weekly PK Competition In Production Workshop
- 9The Second Amateur Football Match of Zhongshan North District in 2017
- 10How to solve the deformation of your prototype and low volume products?