SuNPe offers one-stop services from prototyping to low volume production, which covers the area of car components, home appliances, scientific products, medical devices, electronic products and so on. There are 10 sets of vacuum casting machines at SuNPe to support your project and complete the parts in a very short lead time and cost effective. The following pictures are Drager X-Act 7000 prototype made by vacuum casting at SuNPe and Drager X-Act 7000 product in the market.
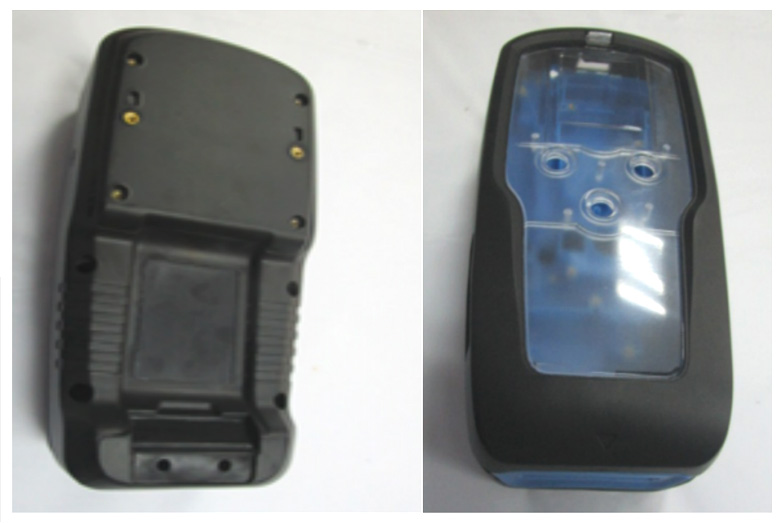
(Drager X-Act 7000 prototype made at SuNPe)
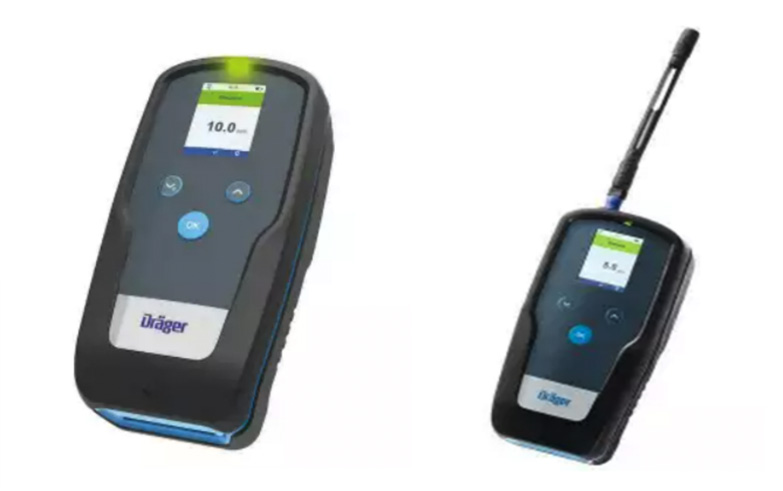
(The Drager X-Act 7000 product)
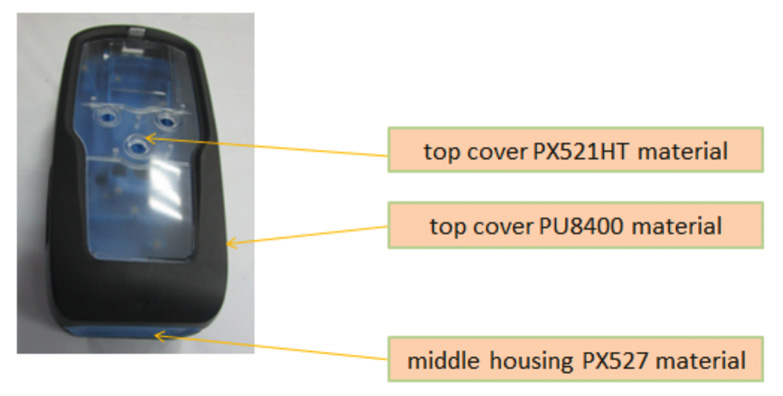
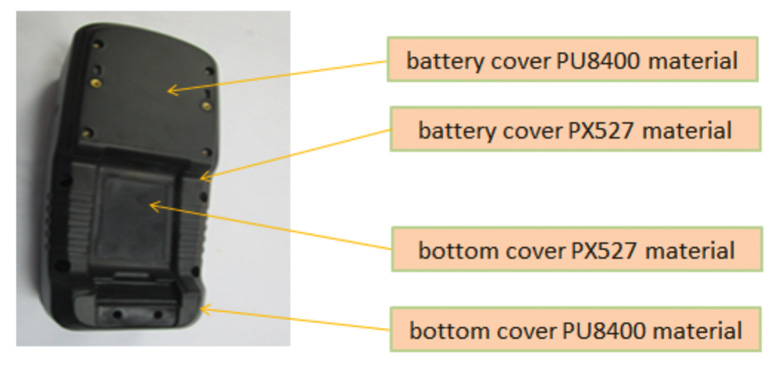
(Materials of Drager X-Act 7000 prototype made at SuNPe)
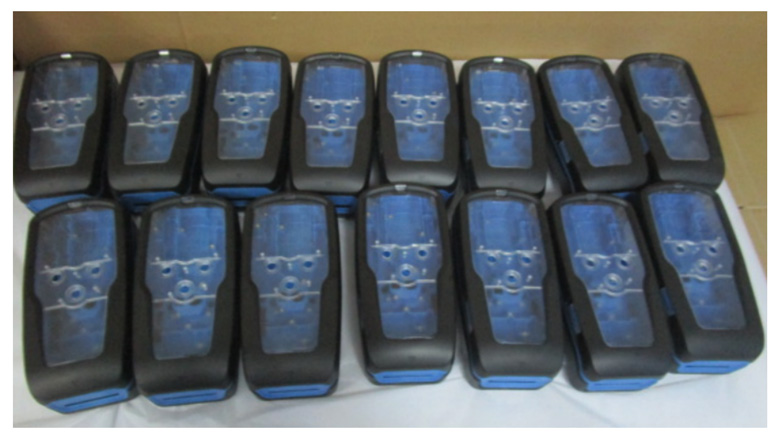
(Assembly Drager X-Act 7000 prototype before shipment)
Our client is very pleased with the Drager X-Act 7000 prototypes and the Drager X-Act 7000 products have been launched into the market smoothly. We are very happy to know this news and we sincerely hope that we can have more chances to help more production into the market in the future and make better world. If there is any quote of vacuum casting project we can help, pls feel free to contact us.
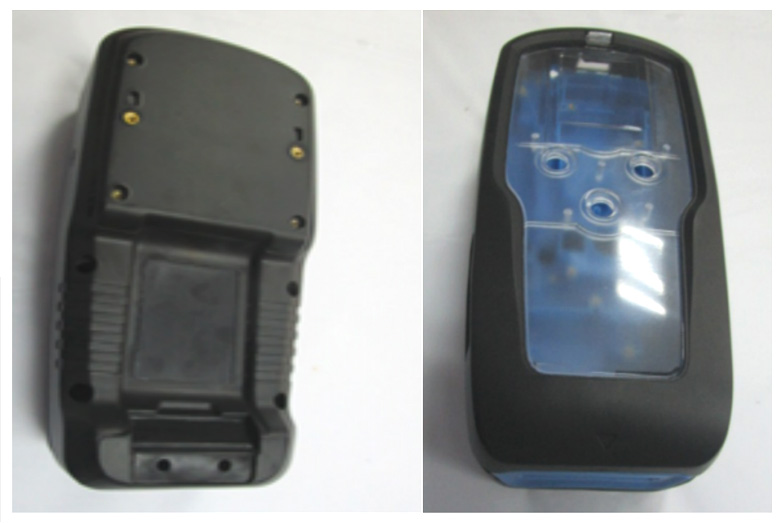
(Drager X-Act 7000 prototype made at SuNPe)
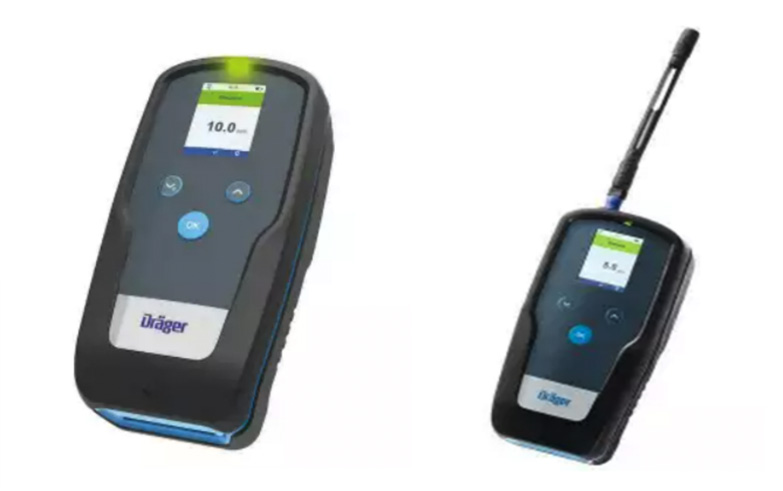
(The Drager X-Act 7000 product)
1.What are the materials used for the Drager X-Act 7000 prototype ?
The Drager X-Act 7000 prototype includes top cover, middle housing , battery cover and bottom cover parts. The material for these parts are PX521HT+PU8400 over-molding, PX527 , PX527+PU8400 over-molding and PX527+PU8400 over-molding. Pls check the pictures of below for each parts’ material.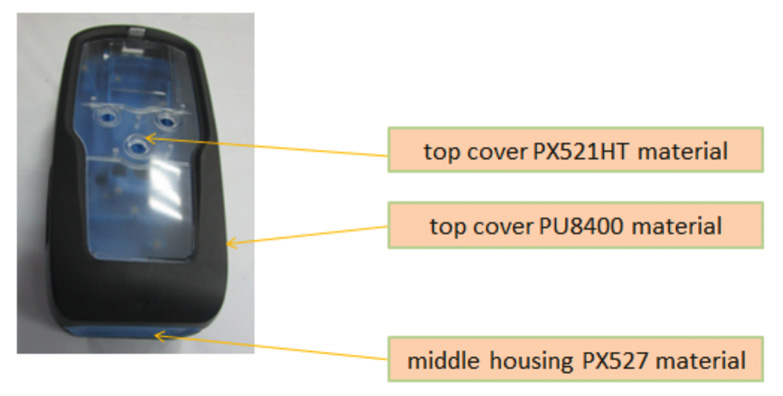
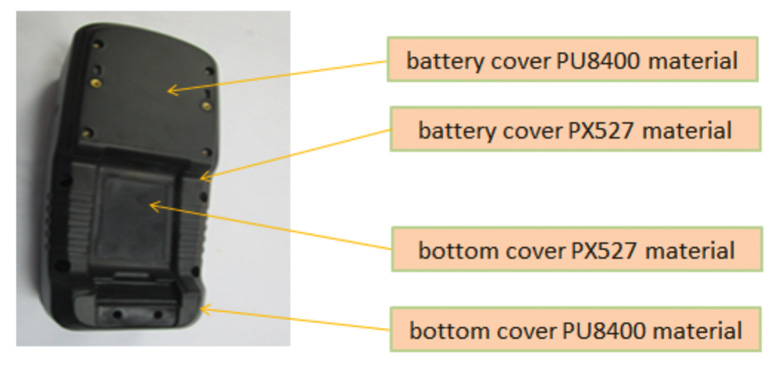
(Materials of Drager X-Act 7000 prototype made at SuNPe)
2.What is the process for making Drager X-Act 7000 prototype ?
There are 5 steps to make Drager X-Act 7000 prototype.Step 1: Vacuum casting the substrate part using PU material. After confirming all the details with our client, we start to make the top cover substrate, bottom cover substrate, battery cover substrate and mid housing in requested material with correct color and texture.
Step 2: Vacuum casting the over-molding parts on the substrate parts. Vacuum casting the top cover over-molding part onto the top cover substrate part, bottom cover over-molding part onto bottom cover substrate and battery cover over-molding part onto the battery cover substrate parts in requested color and texture.
Step 3: Press heat staking the brass inserts into the parts according to installation instructions.
Step 4: Inspected all the prototypes to ensure all the parts are in good quality and assemble all prototypes together before shipment at SuNPe.
Step 5: Pack the products with pearl cotton and then put in the carton, which can ensure the prototypes delivery to our clients in hand safely.
Step 2: Vacuum casting the over-molding parts on the substrate parts. Vacuum casting the top cover over-molding part onto the top cover substrate part, bottom cover over-molding part onto bottom cover substrate and battery cover over-molding part onto the battery cover substrate parts in requested color and texture.
Step 3: Press heat staking the brass inserts into the parts according to installation instructions.
Step 4: Inspected all the prototypes to ensure all the parts are in good quality and assemble all prototypes together before shipment at SuNPe.
Step 5: Pack the products with pearl cotton and then put in the carton, which can ensure the prototypes delivery to our clients in hand safely.
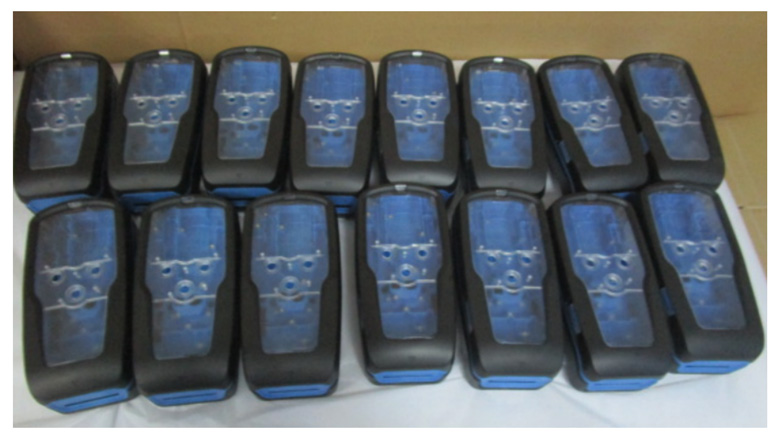
(Assembly Drager X-Act 7000 prototype before shipment)
3. What are the benefits of vacuum casting at SuNPe prototype?
1.High productivity
2.Over-molding
3.Multiple texture options
4.Various PU material
5.Cost effective for small batch production
6.10 sets vacuum casting machines to support your project
7.One-stop services for your finish, such as painting, silk screen, vacuum metalized etc.
2.Over-molding
3.Multiple texture options
4.Various PU material
5.Cost effective for small batch production
6.10 sets vacuum casting machines to support your project
7.One-stop services for your finish, such as painting, silk screen, vacuum metalized etc.
Our client is very pleased with the Drager X-Act 7000 prototypes and the Drager X-Act 7000 products have been launched into the market smoothly. We are very happy to know this news and we sincerely hope that we can have more chances to help more production into the market in the future and make better world. If there is any quote of vacuum casting project we can help, pls feel free to contact us.
Other news
- 1SuNPe Wishes You And Your Family A Happy Mid Autumn Festival!
- 2EMI coating service at SuNPe
- 3Award of Merit for School Development Support
- 4Operation of SuNPe Under COVID-19
- 5Vacuum Casting Is One Of Most Advantages Service at SuNPe
- 6Wire Cutting at SuNPe
- 7The Second Amateur Football Match of Zhongshan North District in 2017
- 8Internal Regular Quality Review Meeting of SuNPe
- 9SuNPe Has Introduced Large Capacity for High Efficiency and Good Quality .
- 10SuNPe plays an important role in the post-epidemic era